
An articulated arm with rigid bones and high precision angular sensors.Such systems work best with flat profile shapes or simple convex curved surfaces. A carriage system with rigid arms held tightly in perpendicular relationship and each axis gliding along a track.The scanner mechanism may have three different forms: Where the object to be scanned is not flat or can not rest stably on a flat surface, it is supported and held firmly in place by a fixture. There are a variety of technologies that fall under each of these categories.Ī coordinate measuring machine with rigid perpendicular arms.Ĭontact 3D scanners probe the subject through physical touch, while the object is in contact with or resting on a precision flat surface plate, ground and polished to a specific maximum of surface roughness. Non-contact solutions can be further divided into two main categories, active and passive.


A well established classification divides them into two types: contact and non-contact. The techniques work with most or all sensor types including optical, acoustic, laser scanning, radar, thermal, and seismic. There are a variety of technologies for digitally acquiring the shape of a 3D object. This whole process, going from the single range map to the whole model, is usually known as the 3D scanning pipeline. These scans have to be brought into a common reference system, a process that is usually called alignment or registration, and then merged to create a complete 3D model. Multiple scans, even hundreds, from many different directions are usually required to obtain information about all sides of the subject. This allows the three dimensional position of each point in the picture to be identified.įor most situations, a single scan will not produce a complete model of the subject. The "picture" produced by a 3D scanner describes the distance to a surface at each point in the picture. While a camera collects colour information about surfaces within its field of view, a 3D scanner collects distance information about surfaces within its field of view. Like most cameras, they have a cone-like field of view, and like cameras, they can only collect information about surfaces that are not obscured. If colour information is collected at each point, then the colours on the surface of the subject can also be determined.ģD scanners share several traits with cameras. These points can then be used to extrapolate the shape of the subject (a process called reconstruction). This 3D model consists of a point cloud of geometric samples on the surface of the subject. The purpose of a 3D scanner is usually to create a 3D model.

4.11 Quality assurance and industrial metrology.4.1 Construction industry and civil engineering.
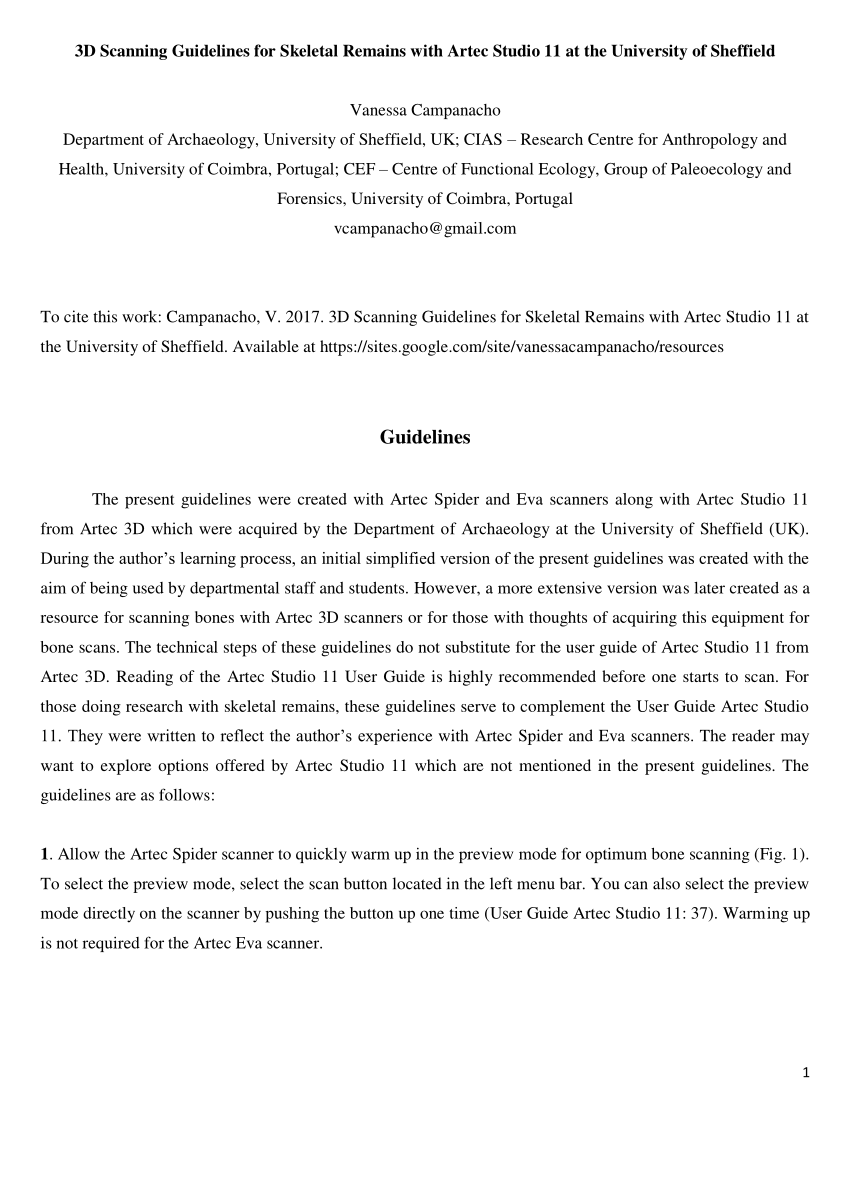
